RDF (Refuse-Derived Fuel) is an innovative and sustainable approach to waste management and energy utilization. It involves converting various solid waste materials into solid fuels through a series of processing techniques.
1. Definition of RDF
RDF stands for Refuse-Derived Fuel, which is a type of fuel made from solid waste that has undergone a treatment process. Typically, RDF has a high calorific value and stable combustion properties, making it suitable to partially or entirely replace traditional fossil fuels like coal and oil. It can be used in industrial production, power generation, and other energy applications.
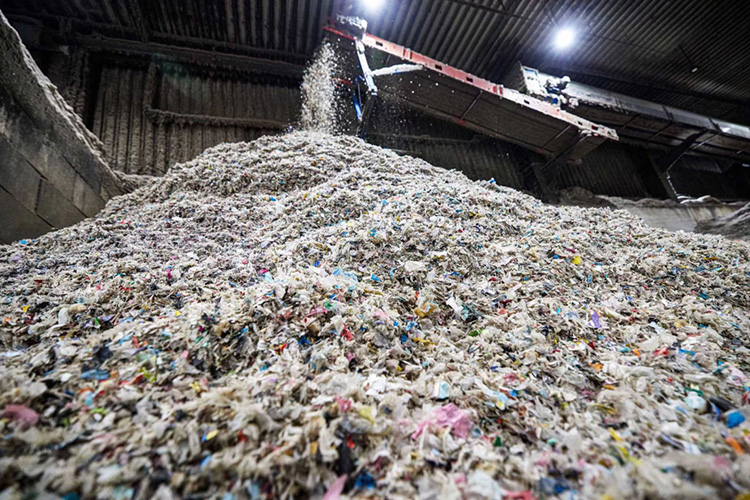
2. Raw Materials for RDF Production
1) Municipal Solid Waste
This includes various waste materials produced in daily life, such as kitchen waste, paper, plastics, textiles, glass, metals, etc. Among these, lightweight, combustible materials such as paper, plastics, and textiles are ideal raw materials for RDF production.
- Advantages: Widely available and in large quantities.
- Challenges: Complex composition and high moisture content, requiring extensive sorting and treatment.
2) Industrial Solid Waste
Examples include light slag from paper mills, leather offcuts from garment factories, and waste fabric from textile production.
- Advantages: Relatively simple composition and high calorific value.
- Challenges: Materials are dispersed, requiring significant collection efforts.
3) Construction and Demolition Waste
This category consists of discarded materials like concrete, bricks, wood, foam, and sponge.
- Advantages: High volume and relatively concentrated waste.
- Challenges: Presence of impurities like soil and rubble, requiring specialized sorting.
4) Biomass Waste
This includes agricultural and forestry residues, such as straw and garden waste.
- Advantages: Simple composition with high calorific value.
- Challenges: Regional limitations, with some areas having abundant sources while others face scattered materials and high transportation costs.
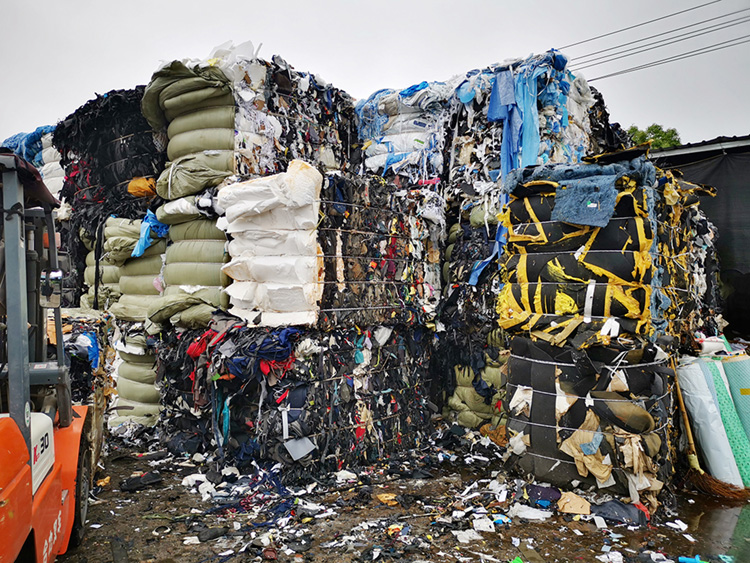
3. RDF Production Process
Shredding
The collected solid waste is first processed by a single-shaft or twin-shaft shredder, which cuts the raw materials into uniform, small particles. This significantly reduces the size of the waste, making it easier for further sorting and recycling.
Sorting
Using equipment like magnetic separation, air separation, and screening, different components such as metals, plastics, paper, and wood are separated from the waste. This enhances the purity of the RDF fuel.
Shaping (Optional)
The dried waste particles can be shaped into specific forms such as blocks or pellets through extrusion or compression. This step improves storage, transport, and combustion efficiency.
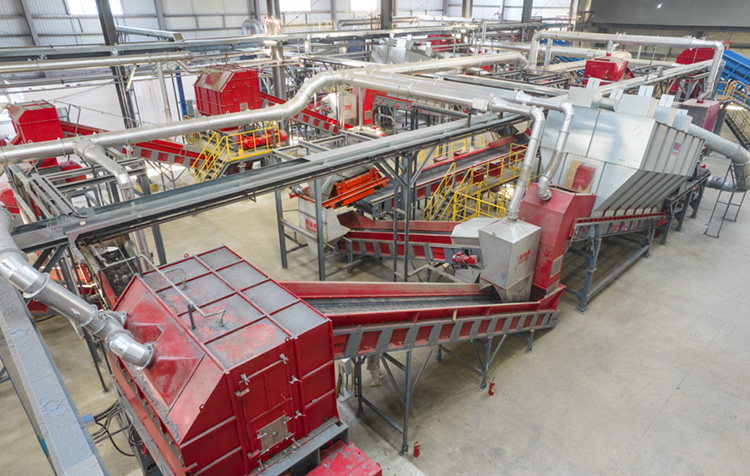
4. Future Prospects of RDF
Environmental Benefits
- Reduced Landfill Use: Converting waste into RDF helps reduce the amount of waste sent to landfills, decreasing land usage and environmental contamination.
- Lower Greenhouse Gas Emissions: RDF produces fewer greenhouse gases compared to traditional fossil fuels, contributing to a reduction in global climate change.
- Reduced Harmful Emissions: When burned in specialized equipment, RDF can minimize the production of harmful substances like dioxins, compared to direct waste incineration.
- Fossil Fuel Substitution: With growing global energy demands and diminishing fossil fuel resources, RDF can serve as a renewable energy source, helping alleviate energy pressure.
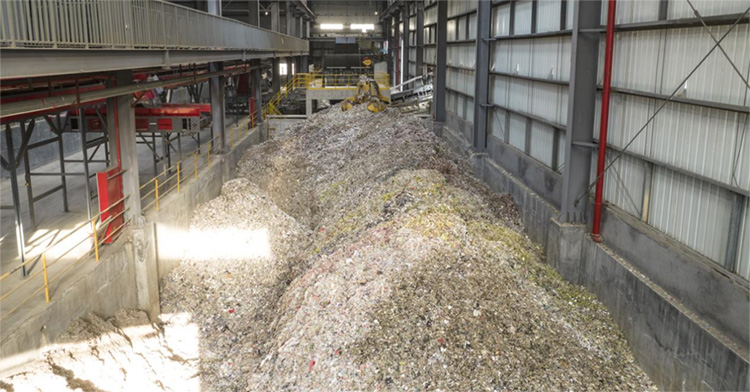
Economic Benefits
- Job Creation: The RDF industry can stimulate related sectors, including waste collection, processing, and manufacturing, creating significant employment opportunities.
- Lower Energy Costs: RDF can be a cost-effective energy source for businesses with high energy needs, reducing energy expenses and improving economic outcomes.
RDF is not only a sustainable solution to waste management but also provides an alternative energy source, addressing both environmental and economic challenges.